Mercedes-Benz accelerates the transformation of its production network by Integrating AI and humanoid robots at its Digital Factory Campus in Berlin
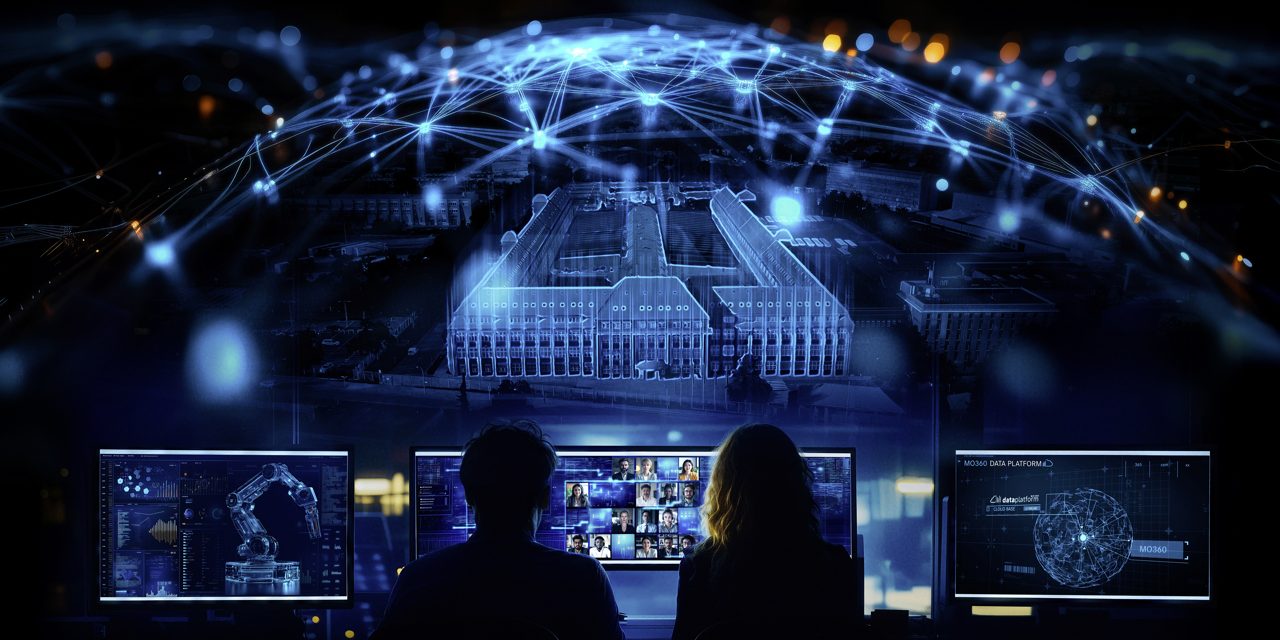
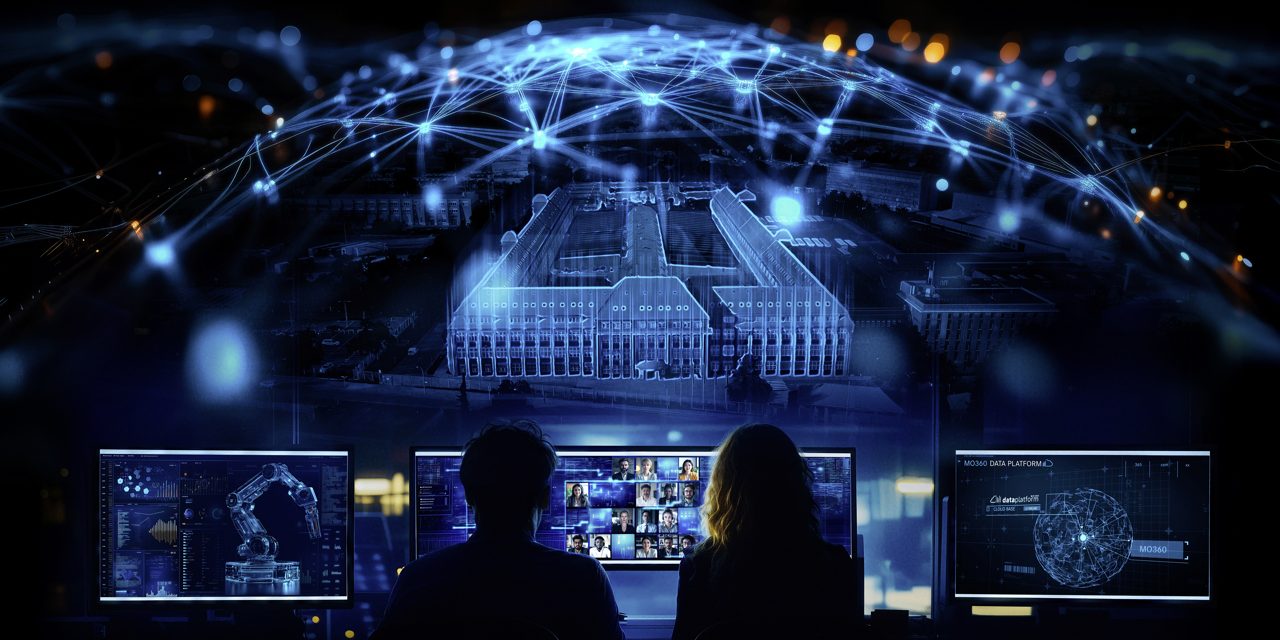
Mercedes-Benz is driving the transformation of its production network by reinforcing Berlin-Marienfelde’s role as the center of innovation for MO360 digital production technologies, now enhanced with Artificial Intelligence (AI), humanoid robots, and pioneering innovations such as the production of high-performance electric axial-flux motors.
In 2022, Berlin-Marienfelde established itself as the global center of expertise for production digitalization through the Mercedes Benz Digital Factory Campus (MBDFC), promoting the development of future software applications in a real-world production environment. The central basis of these endeavors is the Mercedes-Benz Cars Operations 360 digital production ecosystem, or MO360, which contains all the important software applications and data within the global production network. At the MBDFC, the development and testing of new processes and technologies are seamlessly integrated with the swift global implementation of pioneering MO360 software applications for automotive production.
Mercedes-Benz has now enhanced its MO360 production system with AI features, including the Digital Factory Chatbot Ecosystem and the MO360LLM Suite, along with humanoid robots from U.S.-based Apptronik, further establishing Berlin-Marienfelde’s status as a center for global innovation. Today, new production processes and features, including those enabled through the Mercedes-Benz Operating System (MB.OS), are being tested before implementation on real production lines at other Mercedes-Benz assembly plants. Marienfelde, for example, played an important role in preparing the Rastatt plant for its ramp-up of the new Mercedes-Benz CLA, the first vehicle to feature MB.OS, which was unveiled just a few days ago.
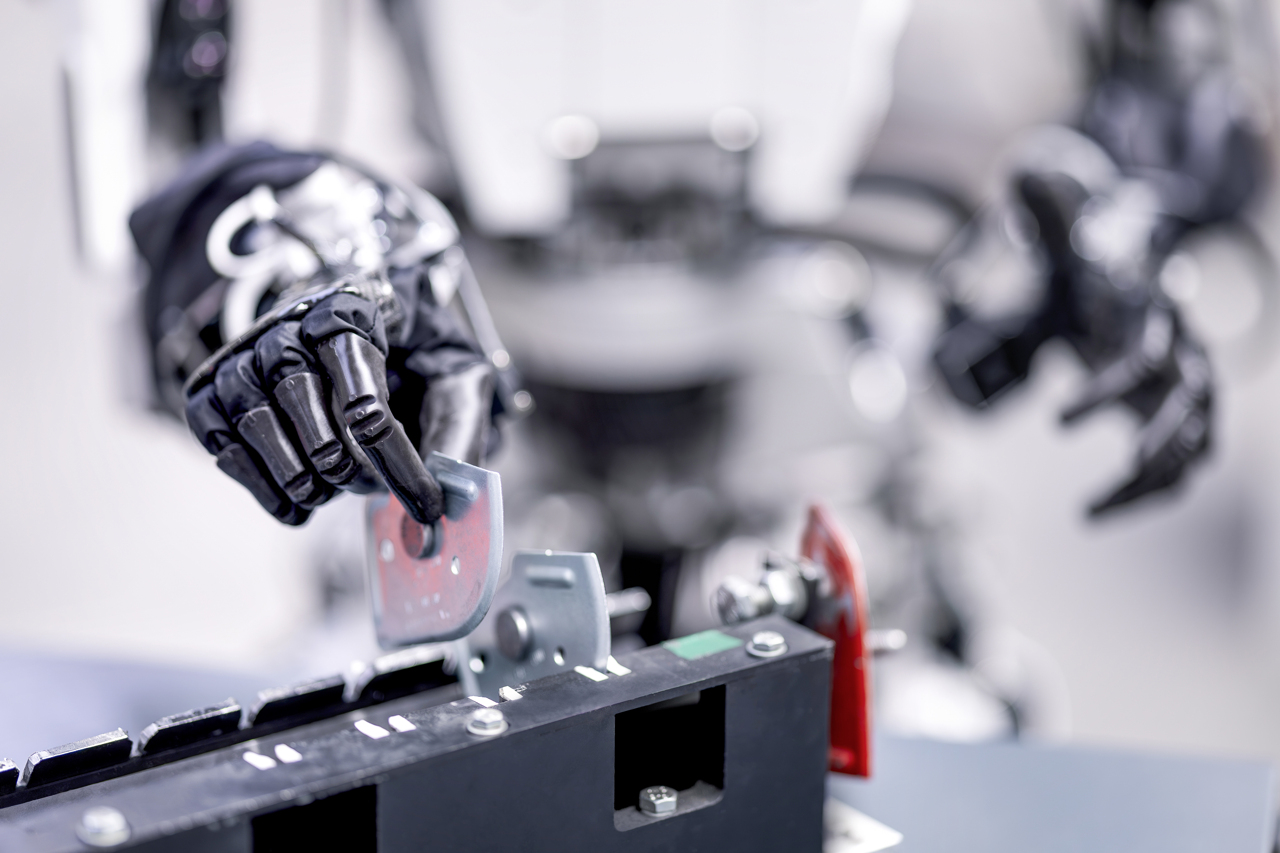
“Mercedes-Benz Berlin-Marienfelde remains at the cutting edge of automotive production and keeps Germany on the map as a global center for innovation. Artificial Intelligence and humanoid robots open up an exciting new frontier which make automotive production more sustainable, efficient and more intelligent.” – Jörg Burzer, Member of the Management Board Mercedes-Benz Group AG. Production, Quality & Supply Chain Management.
Berlin-Marienfelde: proving ground for highly automated robotics in production
Mercedes-Benz is committed to empowering its workforce with state-of-the-art technology, introducing Apollo, one of world’s most advanced commercial humanoid robots, to its manufacturing facilities. To underscore its commitment to deploying humanoid robots in automotive production, Mercedes-Benz will make a low double-digit-million-euro investment into Apptronik, which was founded in 2016 at the Human Centered Robotics Lab at the University of Texas at Austin.
Mercedes-Benz has utilized industrial robotics technology to perform particularly monotonous and physically demanding tasks since the 1970s. The company is currently testing the integration of humanoid robots in production, initially focusing on repetitive tasks within intralogistics. Apptronik’s Apollo can transport components or modules to the production line for Mercedes-Benz’s highly skilled production staff to assemble and conduct initial quality checks on components.
Apollo robots have been collecting data in a production environment to train for specific use cases within MO360. Mercedes-Benz employees with hands-on production experience have transferred their knowledge to Apollo using teleoperation processes and augmented reality. The next significant development at the Digital Factory Campus Berlin involves enabling Apollo’s robots to perform autonomous operations, marking a technological milestone toward a flexible, intelligent assistance system for production.
In December, the AI-powered humanoid robotics company Apptronik announced a strategic partnership agreement with the Google DeepMind robotics team to merge best-in-class artificial intelligence with cutting-edge hardware, advancing humanoid robots to be more helpful to people in dynamic environments.
Artificial intelligence for everyone: smart assistants in everyday production
Artificial intelligence is changing the world, and at the MBDFC, Mercedes-Benz is proactively shaping and developing new smart technologies for the global production network. With the MO360 AI Factory, artificial intelligence is being integrated directly into production, making it intuitive, accessible, and usable for everyone. The in-house “Digital Factory Chatbot Ecosystem” development allows employees to access production databases: Inquiries about machine maintenance or best-practice methods for manufacturing processes can simply be asked via chat, with the AI immediately providing precise answers in multiple languages.
“AI takes over the tasks we usually enjoy less, giving us time to focus on real innovation, creativity and value-adding activities. I’m convinced that it makes a significant contribution to business success when applied strategically and executed pragmatically. So, let’s embrace it as key part of our solution moving forward.” – Katrin Lehmann, Chief Information Officer of Mercedes-Benz Group AG and Mercedes-Benz AG
Another example of the practical use of AI is the virtual multi-agent system. AI-supported virtual assistants analyze complex data in real-time, which, for example, can help to quickly identify the causes of sudden quality deviations in production. Instead of laborious, manual root-cause analysis, engineers rely on AI agents from a virtual data science team. These AI agents quickly and reliably analyze available data, identify patterns and anomalies, and provide well-founded analyses and suggested solutions at the touch of a button, driving real efficiency gains in production.
Transforming Marienfelde with Axial Flux technology
In addition to the development of new production processes, the Marienfelde site has served as an important part of the global powertrain production network for decades, with the production of various drive technologies. As the global automotive industry gradually shifts from combustion-engine technologies to an all-electric future, Mercedes-Benz is establishing Berlin as a center of excellence for the manufacturing of high-tech performance electric motors. Starting next year, the cutting-edge axial-flux motor will roll off the production line at Marienfelde. The production of an axial-flux motor involves approximately 100 processes with around 65 being new to Mercedes-Benz and 35 entirely new to the industry. Innovative applications of laser technologies have been combined with bonding processes and AI, to name just one example. These new production techniques have predominantly been developed in house, resulting in more than 30 patent filings, underscoring Marienfelde’s pioneering role in production process innovations globally.