The next level of efficiency becomes reality for Mercedes
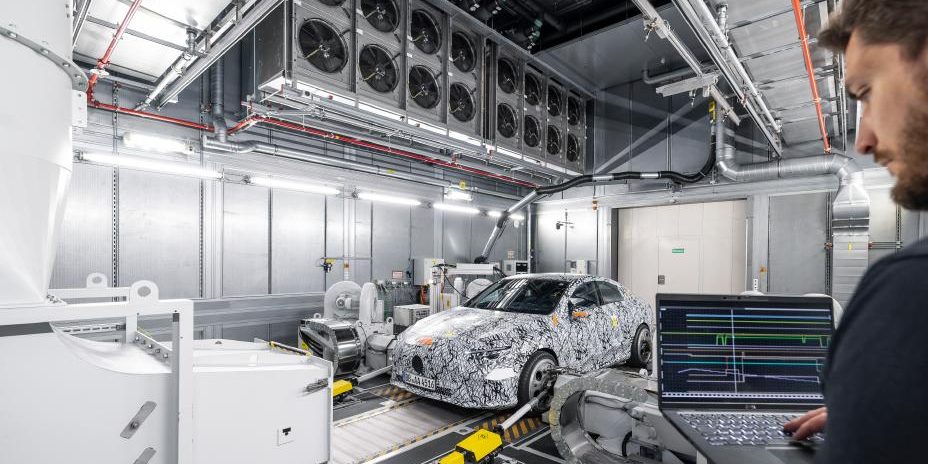
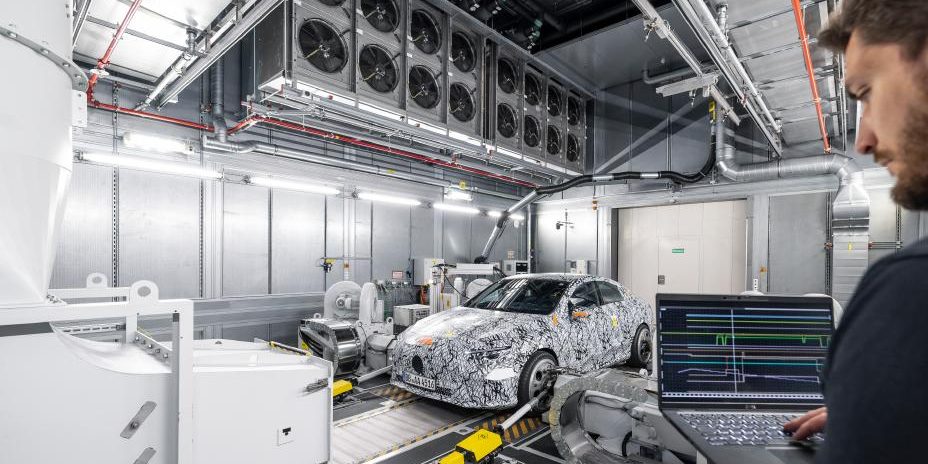
Mercedes-Benz is emphasizing leadership position in drive systems, including those planned for the future. Customers will have the option to choose between two innovative powertrains in the upcoming vehicle architecture. The forthcoming CLA will be offered as a highly efficient electric vehicle and as an economical hybrid.
Mercedes-Benz has set new standards for efficiency with the VISION EQXX technology platform. Now, the company is incorporating insights from this groundbreaking project into its series-production vehicles. Leading the way is the new all-electric CLA, the first model to be based on the Mercedes-Benz Modular Architecture (MMA). At the heart of this versatile and flexible vehicle architecture is the so-called “skateboard” chassis- a floor assembly primarily designed for electric cars, including the corresponding drive and chassis components. While the core architecture remains consistent, the body design will vary. For the U.S., Mercedes-Benz plans a family of three models in total in the newly defined entry-level segment, including the CLA as a four-door sedan and two SUVs.
“As the inventor of the automobile, Mercedes-Benz has always been a pioneer of ground-breaking drive systems. We recently proved this with the record-breaking VISION EQXX technology program. With the upcoming MMA vehicles, we are now making this visionary technology available to our customers and getting ever closer to the idea of the one-liter vehicle of the electric age. Our new hybrid drive with electric transmission is also setting new standards in terms of efficiency. With the new CLA and the other vehicles based on the MMA architecture, all customers will benefit from efficient technology at the highest level.”
Markus Schäfer, Member of the Board of Management of Mercedes-Benz Group AG. Chief Technology Officer, Development & Procurement
Mercedes-Benz will continue to leverage intelligent modularity with a scalable skateboard design for future model families across other segments. With its focus on both electric driving and vehicle software, the company has massively increased its development efforts in these areas. This includes the recent opening of the eCampus in Stuttgart-Untertürkheim, a competence center dedicated for the development of cells and batteries for the future electric vehicles of the brand. The aim is to develop innovative chemical combinations and optimize production processes for high-performance cells with “Mercedes-Benz DNA”, reducing battery costs by more than 30 percent in the coming years.
Parts of the development and testing of the new MMA models have taken place in the Electric Software Hub (ESH). This facility in the Mercedes-Benz Technology Centre (MTC) in Sindelfingen brings together numerous software, hardware, system integration and testing functions under one roof. The entire electrical/electronic integration process of vehicle development is reflected within the ESH ensuring that all new hardware and software components interact smoothly.
The First MMA Model
With its outstanding energy efficiency, the highly flexible MMA architecture marks Mercedes-Benz’s next step toward a fully electric future. The new powertrain reflects the brand’s engineering excellence in both high-voltage components and mechanical systems such as transmissions. The Electric Drive Unit (EDU 2.0) is the first of a new generation of electric drive units from Mercedes-Benz, designed as a highly integrated modular system.
With the main drive on the rear axle for optimum traction and handling, Mercedes‑Benz is now introducing a drive configuration traditionally seen the mid-size and luxury-class vehicles to the entry-level segment. The 200-kW electric drive unit, featuring a permanently excited synchronous machine (PSM) on the rear axle, was developed entirely in-house by Mercedes-Benz engineers. High-performance power electronics are equipped with a silicon carbide (SiC) inverter for particularly efficient energy utilization. Both transmission control and inverter are integrated into a single component. The drive unit is built in Untertürkheim, where Mercedes‑Benz has developed many innovative drive systems over the years.
The EDU 2.0 strikes a perfect balance between maximum torque, top speed and exemplary efficiency, especially in real-world driving conditions. The high torque ensures dynamic driving performance, whether tackling mountain passes or towing trailers. Another advantage is the extraordinary compact design of the EDU 2.0, which benefits the interior dimensions and the rear trunk volume.
For 4MATIC models4, an 80-kW drive unit in mounted on the front axle. Designed with efficiency in mind, this unit is equipped with a next-generation silicon carbide (SiC) inverter and designed as a permanently excited synchronous machine (PSM). The front electric motor acts as a “boost” drive, engaging only when the corresponding power or traction is required. This task is performed by the Disconnect Unit (DCU), which Mercedes-Benz is introducing for the first time in the entry-level segment.
For greater efficiency, the DCU can decouple the electric motor on the front axle at lightning speed when demand is low, so that the electric motor and parts of the transmission are at a standstill. This reduces front axle losses by up to 90 % and increases driving range. In the case of the Concept CLA Class, this would correspond to a range of more than 750 kilometers (466 miles) (WLTP)5. With an energy consumption of just 12 kWh/100 km (5.2 mi/kWh), the Concept CLA Class would embody the ‘one-liter car’ of the electric age.
Mercedes-Benz is introducing 800-volt electrical architecture for the first time, maximizing both efficiency and performance. In conjunction with the new battery generation, this system can significantly reduce charging time. In just 10 minutes, the Concept CLA Class can gain a range of up to 300 kilometers (186 miles)6 via using DC fast charging. Thanks to its focus on time efficiency, the CLA has already outperformed other close-to-production electric vehicles in a record attempt: In a 24-hour test drive at Nardò in southern Italy, a pre-series model covered exactly 3,717 kilometers (2,309 miles) in 24 hours. The two-speed transmission on the main drive on the rear axle not only contributes to efficiency, but also enables extremely dynamic driving performance.
The cells of the premium battery with a usable energy content totaling 85 kWh have anodes in which silicon oxide is added to the graphite. Compared to the predecessor battery with conventional graphite anodes, the gravimetric energy density is up to 20 % higher. At cell level, the volumetric energy density of the cell chemistry is 680 Wh/l (watt-hour / liter). Raw material usage has been further optimized and reduced to enhance sustainability, particularly with a significant reduction in the proportion of cobalt.
The New Hybrid is Capable of All-Electric Driving
Mercedes-Benz is reaffirming its leadership in drive systems – whether electric or hybrid. Efficiency is also the key to modern hybrid drive system development. Vehicles built on the MMA architecture will also be offered as hybrids with 48-volt technology. The electric motor with 20 kW drive power 7 has been integrated into a new electrified eight-speed dual-clutch transmission (8F-eDCT) together with an inverter. Electrical energy of up to 1.3 kWh is provided by a new 48-volt battery with lithium-ion technology and a flat-pack design.
Thanks to energy recuperation and the ability to drive all-electric at urban speeds, this drivetrain is particularly efficient. This is enhanced by electric coasting at a speed of up to approximately 100 km/h (62 mph)3. The combustion engine is a new FAME (Family of Modular Engines) four-cylinder petrol engine. The hybrid drivetrain will be available with 140 kW output at launch in the U.S.
The One-Liter Car of the Electric Age
Insight Mercedes-Benz Drivetrains & Efficiency: The Efficient Electric Drive
- 800-volt system and two-speed gearbox in the entry-level segment for the first time
- Main drive developed and produced entirely by Mercedes-Benz
- Long-range efficiency of 93 % underscores extremely high overall performance
- New drivetrain has potential to achieve consumption of around 12 kWh/100 km (5.2 mi/kWh) and a WLTP range of over 750 km (466 mi)
- Navigation with Electric Intelligence12 offers accurate real-time energy forecasts
The new CLA is the trailblazer for the upcoming lineup of Mercedes-Benz electric vehicles that will soon go into series production. Key innovations include the 800-volt electric architecture and the advanced drive units including a two-speed gearbox on the main drive at the rear axle. Derived directly from the ground-breaking technology of the VISION EQXX, the new Electric Drive Unit (EDU 2.) has been fully developed in-house. Additionally, the 4MATIC models8 feature a Disconnect Unit (DCU) on the front axle. The 800-volt system maximizes both efficiency and performance and can significantly reduce charging times. In the Concept CLA Class, a 10-minute charge can add a range of up to 300 kilometers (186 miles). 9
A Drive System Based on the VISION EQXX Technology Platform
The new drive system is capable of achieving a range of more than 750 kilometers (466 miles) (WLTP)4. For the Concept CLA Class, this translates to an energy consumption of approximately 12 kWh/100 km4 (5.2 mi/kWh) – earning it the title of the “one-liter car of the electric age”. The battery-to-wheel efficiency over long distances is an impressive 93%4.
The compact, up to 200 kW electric drive unit with a permanently excited synchronous machine (PSM) on the rear axle was developed entirely by Mercedes-Benz engineers at the Untertürkheim facility, where the company has developed many innovative drive systems over the years. The rotor magnets are arranged in a double-V shape. Another feature is the winding of the stator with so-called stretched coils. Together, these measures contribute to a remarkably quiet driving experience. The PSM also uses a significantly less rare earth materials than previous motor generations, reducing the proportion of heavy rare earths to almost down to zero per cent. High-performance power electronics feature a silicon carbide inverter for particularly efficient energy utilization.
The architecture also includes a two-speed gearbox on the rear axle, offering a blend of dynamics and efficiency. The first gear, with a short ratio of 11:1, provides excellent acceleration right from the start and outstanding efficiency in urban driving. The second gear (gear ratio: 5:1) is optimized for power delivery at high speeds and for high efficiency on the highway allowing a top speed of up to 210 km/h4 (130mph). The shift points depend on the driving situation and the selected driving program. The online optimizer continually adapts them to current parameters such as battery SoC, performance and driver requirements. Traction is achieved via claws (1st gear) or discs (2nd gear). The transmission has special thermal insulation.
The 4MATIC models7 are equipped with an 80-kW electric motor on the front axle. To maximize efficiency, this motor also incorporates a next-generation inverter with silicon carbide (SiC) and is designed as a permanently synchronous machine (PSM). The front electric motor acts as a “boost” drive only engaging when the corresponding power or traction is required. This task is performed by the so-called disconnect unit (DCU), which Mercedes-Benz is now using for the first time in the compact class. For further efficiency, the DCU can decouple the electric motor on the front axle at lightning speed when demand is low, so that the electric motor and parts of the transmission are at a standstill. This reduces front axle losses by 90% and increases the range.
This highly efficient system also allows for a front trunk (frunk), while ensuring a high level of crash safety via a predetermined bending point on the frame. The EDU is connected to the body via two elastomer bearing levels and an additional support frame. This elaborate double structure-borne noise decoupling, among other things, results in excellent NVH (noise, vibration and harshness) behavior.
Ultra-Fast Charging with Up to 320 kW Power
In conjunction with the premium version of the battery, the 800-volt configuration enables high-power DC charging at up to 320 kW10. The premium battery design ensures that this high charging power is maintained over a broad state-of-charge range, enabling short stops. The Concept CLA Class has already demonstrated that 10 minutes of charging can add up to 300 kilometers (186 miles) in range11.
If Electric Intelligence12 navigation is activated, the battery is preheated during the journey if necessary. The systems preconditioning allows for the battery to reach the optimum temperature for fast DC charging at the charging point.
For AC charging, the system offers 11 kW chargers. Mercedes‑Benz relies on a highly integrated “one-box” system in a lightweight design for the charging technology – a technology transfer from Formula 1.
In the future, new entry-level models will feature bidirectional charging13. When connected to a compatible bidirectional DC charger, the vehicle then becomes an energy storage system that can store solar power for later use, for example, or even serving as an electricity supplier to a home (V2H) or the grid (V2G).
Simultaneous Use of Three Energy Sources: New Multi-Source Heat Pump
The MMA models will be the first Mercedes‑Benz vehicles to feature an air-to-air heat pump as standard- no longer taking the indirect route via a water circuit. This multi-source heat pump can utilize three energy sources in parallel: the waste heat from the EDU 2.0, waste heat from the battery, and ambient air.
Maximum Recuperation and Minimum Energy Consumption
Intelligent recuperation contributes to achieving high efficiency, with recuperation power potentially reaching up to 200 kW. The majority of braking operations in everyday driving are carried out with the aid of recuperation rather than mechanically via the wheel brakes. In fact, the vehicle can even come to a complete stop using only regenerative braking and thus recover kinetic energy. The strong deceleration (up to 3 m/s4 per axle) means more recovered energy and therefore, a longer range. Recuperation is even possible in ABS mode or on icy roads.
The selector lever behind the steering wheel can be used not only to select the gear, but also to adjust the recuperation power. Pulling the lever towards the steering wheel causes the recuperation level to increase to a deceleration of up to 3 m/s4. Pushing the lever away towards the driver’s display, on the other hand, reduces the energy recuperation level. By pressing the selector lever again, the driver switches between the recuperation levels D + and D Auto. The lower area of the display indicates which lever is selected.
The four recuperation levels:
- D Auto: Intelligent recuperation
- D+: No recuperation (sailing)
- D: Standard recuperation (up to 1 m/s4)
- D-: Increased recuperation (up to 3 m/s4)
All four recuperation levels can be set as “Last Mode”. ECO Assist is automatically active in recuperation level D Auto. Depending on the features, the ECO Assistant uses the data stored in the navigation map as well as information from sensors and cameras to determine the vehicle’s expected route. This enables the system to optimize the driving style for the upcoming conditions, minimizing energy consumption and maximizing recuperation. The following route events can be recognized: roundabout, sharp bend, junction, T‑junction, downhill gradient and speed limit. The ECO Assistant can also react to other junctions or turn-offs if the indicator is activated in time.
If the system detects an incident or vehicle ahead, and your own vehicle is approaching it, the ECO Assistant calculates the optimized speed profile based on distance, current speed, and available route information. The “Foot Off Accelerator” indicator then appears in the display, positioned even more centrally in the new generation of electric cars. If the driver responds, intelligent recuperation is activated in overrun mode. If the ECO Assistant detects a vehicle or a stationary object in front, it can even bring the vehicle to a complete stop, such as in a traffic jam or at traffic lights.
Continuous Development Makes Predictive Energy Management Even More Realistic
When it comes to navigation with Electric Intelligence12, the system does exactly what the name implies. It plans the fastest and most convenient route, including charging stops, based on numerous factors, and adjusts dynamically to traffic jams or changes in driving style, for example. This convenient system, familiar from the EQS and EQE, has been enhanced for the new generation of electric cars. Mercedes-Benz is continuously refining energy forecasting for navigation with Electric Intelligence12. In future, the predicted wind conditions along the carriageway will be taken into account even more precisely based on the vehicle’s height.
While conventional range calculators rely on historical data, navigation with Electric Intelligence12 anticipates future conditions. The system computes energy requirements during route planning, considering topography, route, ambient temperature, speed, heating and cooling requirements as well as traffic situation on the planned route. It also factors in available charging stations, their capacity and the payment functions. The calculation takes place in the cloud and is combined with onboard data.
Customers do not necessarily need to fully charge at every charging stop, but instead will receive a specific recommendation for the optimum charging time at each station. The system schedules stops to optimize the overall journey time- sometimes, two shorter, higher-capacity charging sessions may be preferable to a single long stop. In addition, the vehicle’s charging settings are automatically adjusted by the Electric Intelligence12 navigation system and maximize fast charging along the route.
The MBUX system visualizes the current battery capacity, enabling drivers to see if they can return to the starting point without charging. Manually added charging stations along the way are prioritized in the route calculation, while suggested charging stations can be excluded. The system also estimates the cost of each charging stop.
If there is a risk of not reaching the destination or the next charging station, the range monitoring system supports the driver by displaying the maximum driving speed required to reach the destination. It also provides energy-saving tips. Under the “Range” menu item, the driver can switch off various energy consumers to increase the range and activate the ECO driving functions to support a more efficient driving style.
New Cell Chemistries: High Energy Density, Fast Charging and Excellent Performance
Insight Mercedes-Benz Drivetrains & Efficiency: Battery Expertise
- Modular high-integration concept with compact battery design
- Premium battery version with up to 85 kWh usable energy capacity and silicon oxide anode available at launch in U.S.
- Meets the highest Mercedes-Benz safety standards
Cell chemistry plays a fundamental role in determining the performance of the battery and is also ultimately the defining factor for the entire drivetrain characteristics. The VISION EQXX technology program demonstrated how mastering cell chemistry is key for the development of future products. With its high-performance battery based on pioneering cell chemistry, the EQXX has set several EV track records. With its high energy density and fast-charging capability, the new battery generation is taking these successes to the next level. At the same time, battery costs have been reduced by as much as 30%.
By developing the battery software in-house, Mercedes-Benz has been able to shape the brand’s characteristic driving experience. Data transparency throughout the development phase ensures highest quality, while the in-house approach underscores Mercedes-Benz’s position as a leader in vehicle software.
Modular Architecture
The innovative battery system in the new Mercedes-Benz EV generation is based on a modular, high-integration concept. The repairable battery comprise four large cell modules with hardcase cells and are characterized by a compact and flat design.
The premium battery, with a usable energy content totaling 85 kWh, will be available at launch in the U.S. It features anodes in which silicon oxide is added to the graphite, which improves the gravimetric energy density by up to 20% compared to conventional graphite anodes. The volumetric energy density of the cell chemistry is 680 Wh/l (watt-hour/liter), and the proportion of cobalt has been further reduced.
Intelligent Thermal Management
The high-voltage battery is integrated into the intelligent thermal management system of the all-electric MMA models ensuring it always operates within an optimal temperature range, even in freezing cold or extreme heat. The system is equipped with a liquid cooling system, with an auxiliary heater integrated into the water circuit. At low temperatures, the heater warms the cooling water, which then circulates through the high-voltage battery to heat it, optimizing performance and efficiency.
When Electric Intelligence14 navigation is activated, the battery is preheated during the journey if necessary. This preconditioning allows it to reach the optimum temperature at the fast DC charging point, which can charge the premium battery type at an output of 320 kW adding up to 36 kWh in just 10 minutes15.
Extensive Safety Measures
The battery housing is integrated into the vehicle’s structure and the crash-safety system. All high-voltage (HV) components, including cables and the battery itself, are designed and protected to meet the stringent safety standards of Mercedes-Benz. In addition to the legal requirements, both the entire vehicle and the battery must pass internal testing standards that are sometimes stricter.
In the pole impact test, one of the Group’s own crash tests, electric vehicles are not only tested to ensure that the side structure offers maximum protection to occupants, but also examined for the deformation behavior of the battery. In this crash test configuration, the test vehicle is on a sled and crashes sideways against a steel pole. Mercedes-Benz uses another special test bench to simulate the so-called “touchdown management” which refers to the design precautions taken to prevent damage to the underbody caused by touching down, for example when driving over curbs. During the test, a ram is pressed into the vehicle floor with several tons of force. This also tests whether there is a risk of intrusion from foreign objects lying on the road, such as lost towbars.
Mercedes-Benz has further improved the already very high safety standard of the batteries with technical solutions for the new battery generation used in the MMA models. Precautionary measures have been implemented to prevent potential thermal reactions by ensuring appropriate spacing between the battery cells and the structure of the cells and cell modules. In addition to alerting the occupants in the event of an issue, the advanced early warning system in this model family also includes additional vehicle-side protective measures – for example, automatic closing of side windows and ventilation flaps. A new sensor, centrally located within the battery, continuously monitors the batteries of Mercedes-Benz vehicles even when they are switched off.
Each battery is subjected to a pressure test at the end of production and the battery housings are subject to additional testing. To verify comprehensive anti-corrosion measures, they are exposed to salt water, among other things.
The multi-stage protection concept of the high-voltage (HV) system has already demonstrated itself in other all-electric models from Mercedes-Benz. Real-world accident analyses conducted by Mercedes-Benz Accident Research have confirmed that safety in vehicles bearing the three-pointed star is not dependent on the drive system. In the event of an emergency, the HV system can be automatically deactivated and disconnected from the battery. There are two types of disconnection: reversible and irreversible. Reversible disconnection occurs in minor accidents, where the high-voltage system can be safely reconnected after an insulation measurement carried out by the vehicle confirms no faults. This ensures that the vehicle, if still roadworthy, can continue to be driven. In the event of more serious accidents, the high-voltage system is irreversibly switched off, typically when the vehicle is no longer drivable. It cannot be reactivated without repair in a specialized workshop. When the system is deactivated, it ensures that no residual electrical voltage is present in the high-voltage system outside the battery within a few seconds. Disconnection points are also provided for the emergency responders to deactivate the high-voltage system manually.
New Center of Excellence for The Development of High-Performance Cells, Global Production Network
Mercedes-Benz recently strengthened its battery technology development with the launch of the eCampus in Stuttgart-Untertürkheim. This new center of excellence is dedicated to advancing innovative chemical combinations and optimizing production processes for high-performance battery cells with “Mercedes-Benz DNA”. The expertise gained at the eCampus will influence the technology development and series production of battery cells at the partner companies for use in future Mercedes-Benz battery generations.
Batteries for the all-electric Mercedes-Benz vehicles are manufactured in the global battery production network. The Kamenz battery factory will be the first factory in this network to produce batteries for the new MMA platform models. The cooperation with different cell suppliers worldwide is in line the “local-for-local” approach.
MMA Hybrid Models Capable of Energy Recuperation and All-Electric Driving
Insight Mercedes-Benz Drivetrains & Efficiency: New Self-Developed Combustion Engine Drivetrain
- Efficient hybrids featuring 48-volt technology can drive electrically at city speeds
- New four-cylinder FAME engine family with Miller combustion process
- Newly developed electrified eight-speed dual-clutch transmission with integrated electric motor
- New 48-volt flat pack with 1.3 kWh of energy content
Fully electric models play a key role in implementing the Mercedes-Benz sustainable business strategy. However, the preferences and mobility needs of customers across the globe determine the pace of this transformation. The new model family will therefore also be available as a hybrid with 48-volt technology and an electric motor with 20 kW drive power integrated into the transmission. The highly efficient drivetrain was developed by Mercedes-Benz engineers in Germany adhering to the brand’s rigorous quality standards.
The impressive compactness of the motor and gearbox design can be attributed to the close proximity of the cylinders and the side-by-side arrangement of the integrated electric motor. The motor, inverter, and transmission together form a highly integrated unit. A newly developed 48-volt battery with lithium-ion technology offers an energy content of up to 1.3 kWh. The design is exceptionally compact integrating the battery cells and the DC/DC converter into what is known as a flat pack.
The electric motor provides intelligent support in the low-speed range. The constant speed profiles are covered electrically, meaning that this operating mode will eliminate inefficient operation. Recuperation and the ability to drive purely electrically at urban speeds enhance the drivetrain’s efficiency. Additionally, electric coasting is possible at speeds of up to approximately 100 km/h (62 mph). A special feature: the engine can recuperate in all eight gears, recovering up to 25 kW of energy.
Due to the additive torque characteristics of the combustion engine and electric motor, the maximum torque is achieved over a wide speed range. In addition, the combustion engine can be started entirely via the electric motor and separating clutch eliminating the need for a conventional pinion starter. The start-stop function makes engine starts nearly imperceptible for the driver.
The electric motor and inverter are integrated into a new, highly compact eight-speed dual-clutch transmission (8F-eDCT). This development is knows as “eDCT” because the electric motor is integrated into the transmission and the mechanical system is controlled electrohydraulically. An electric motor operates both dual clutch lines. Power is connected and disconnected with the aid of two drive clutches and a separating clutch. The ratios of the eight gearshift stages are widely spread, which allows the engine operating points to be optimized for better efficiency.
The combustion engine is a newly developed Mercedes-Benz four-cylinder petrol engine with a displacement of 1.5 liters. The unit with the type designation M 252 belongs to the FAME (Family of Modular Engines) family designed for a wide range of vehicle applications. Common features of the FAME engine family include an all-aluminum crankcase with NANOSLIDE® technology, a cylinder head with partially integrated manifold and a turbocharger with segment turbine with switchable scroll connection. Other highlights include the compact charge air duct and the exhaust system positioned close to the engine in one-box design, which is prepared for future exhaust emission standards.
The concept of the electric refrigerant compressor with 48-volt technology adopted from the M 256 reduces frictional power and enables the vehicle to be air-conditioned even when stationary and in all-electric operation.
The hybrid drivetrain will be available with 140 kW output at launch in the U.S. paired with 20 kW of electric drive power. 16 Given the engine’s displacement of 1,496 cm3 (91.1 in3), this represents a considerable output per liter. Buyers will have the choice between front-wheel drive and 4MATIC all-wheel drive17.
For reasons of efficiency, the petrol engine uses a combustion process based on the Miller cycle keeping fuel consumption low, especially in the partial load range – a very common driving scenario in everyday use. The comparatively early closing of the intake valves reduces throttle losses and enables a high compression ratio of 12:1.
The new engine-transmission unit has compact dimensions and is installed transversely in the vehicle between the steering knuckles. A key advantage is the exceptional NVH (Noise, Vibration, Harshness) performance. The M 252 engine naturally has an advantage, because Mercedes-Benz uses four cylinders instead of three. In addition, the engine is equipped with a comprehensive NVH package consisting of foams and covers to further minimize noise emission.
The double bulkhead insulation concept, familiar from higher vehicle classes, has also been extended to the side area of the A-pillar and the floor area for even quieter operation.
New 24-hour World Record in Nardò: Impressive Endurance Test
Insight Mercedes-Benz Drivetrains & Efficiency: Behind The Scenes
- A distance of 3,717 km (2,309 mi) was covered on the high-speed track
- This corresponds to the distance from Trondheim (Norway) to Istanbul (Turkey)
- A total of 40 charging stops were made, each lasting around 10 minutes
- Extensive digital simulation in advance and live telemetry made this achievement possible
- Electric Software Hub served as the epicenter of digital research and development
How many miles can an all-electric CLA cover in 24 hours, factoring in charging stops and driver changes? That was the challenge posed by the development team tasked with optimizing the efficiency of Mercedes-Benz’s new all-electric compact class models. The impressive answer was provided by “Project N”, the internal code name for a project that is as secret as it is ambitious. “N” stands for Nardò, the location of the highspeed track in southern Italy where, in April 2024, two close-to-production prototypes of the CLA set out to achieve a remarkable feat.
One CLA covered exactly 3,717 kilometers (2,309 miles) within 24 hours – surpassing the performance of other near-production electric vehicles The distance of the endurance run is equivalent to a trip from Trondheim (Norway) to Istanbul (Turkey). Air temperatures ranged from 55.4°F at night to 84.2°F during the day. The temperatures of the tarmac were even higher.
The vehicle’s battery was charged exactly 40 times at a standard charging station during the 24-hour test, with each stop only lasting around 10 minutes. Despite these stops, the average speed was a remarkable 154.9 km/h (96.2 mph). In the preparation for the drive, the experts at Mercedes determined the ideal charging strategy to maximize the average speed. On a real long-distance journey, this optimization takes place via navigation with Electric Intelligence18.
As with the three road trips of the VISION EQXX technology carrier, this 24-hour drive also relied on live telemetry: Real-time sensor data was transmitted from the circuit to the nearby mission control room, where it was compared directly with the simulation data and then used for further optimization. This continuous feedback loop allowed the team to react to environmental influences and temperature changes and adapt the strategy via simulation and optimization. Drivers received appropriate instructions via radio to enable them to implement the adjustments in strategy. The dashboard and the data from the live telemetry could be used by colleagues worldwide and were also analyzed by teams in Stuttgart and Sindelfingen.
In the preparation phase, Digital simulations were carried out, where data from several test drives was utilized . This was followed by extensive test bench runs. In the week prior to the actual endurance test, the car covered over 7,000 kilometers (4,349.6 miles) on a vehicle drive test stand in different climatic conditions. The “lessons learned” strategy also included conversations with former Nardò record holders who drove for Mercedes-Benz. Among them was Robert Schäfer, who set three world records in 1983 with a Mercedes 190 E 2.3 16V over distances of 25,000 kilometers (15,534 miles), 25,000 miles and 50,000 kilometers (31,068.8 miles) and set nine international class records.
“Our 24-hour drive in Nardò demonstrated the high time efficiency of our new, compact generation of electric cars on long journeys. The vehicles have also proven their maturity a good year before market launch. At the same time, the successful test is of course very encouraging for the entire company.”
Markus Schäfer, Member of the Board of Management of Mercedes-Benz Group AG. Chief Technology Officer, Development & Procurement
The interdisciplinary composition of the “Project N” team, with specialists from series development and complete vehicle development as well as data experts, was key to the success of the test. While only a small core team was on site in Nardò, they always knew that they had the full support of the colleagues at the Sindelfingen and Untertürkheim offices.
Electric Software Hub (ESH): The Epicenter of Digital Development
The Electric Software Hub (ESH), which opened in 2022, played a crucial role in the development of the new generation of compact electric cars from Mercedes-Benz. Located at the Mercedes-Benz Technology Centre (MTC) in Sindelfingen, the ESH brings together numerous software, hardware, system integration and testing functions under one roof. The entire electrical/electronic integration process of vehicle development is reflected inside the ESH. This integrated approach ensures that all new hardware and software components interact smoothly.
From top to bottom – from code to product – software and hardware continue to flow into the vehicle until they are integrated into vehicle prototypes on the lower floors. Software code creation and pre-integration laboratories are located on the upper floors. Here, the experts first use virtual technologies and simulation to test whether the various software components interact correctly with each other and whether the vehicle functions are implemented without errors. This process is known as integration. State-of-the-art safeguarding methods for electrics/electronics are used here. For example, components and control units in a virtual vehicle are tested fully automatically (“hardware-in-the-loop”). In this approach, only electronics with software to be tested are actually present, while the vehicle and its environment are simulated.
With the “digital test drive”, a test in the vehicle can be fully simulated in the ESH. In a fully simulated environment, a virtual vehicle is moved and tested in the same way as it would be in a real test drive – only this “test drive” takes place in a laboratory on the sixth floor of the Electric Software Hub.
Vehicle-Related Testing Without a Vehicle: The Innovative Test Benches
The ground floor of the ESH in Sindelfingen is home to many high-tech test facilities such as roller and climate test benches. The so-called full vehicle system test bench (FVS) stands out with its innovative concept. It combines a high-voltage drivetrain with a functional mock-up of the 12-volt vehicle electrical system. Both superstructures are located in adjacent rooms and are connected to each other via a cable harness – an umbilical cord, so to speak. Built in a framework of metal profiles, all vehicle components can be assembled, connected and tested in the overall system in this open structure without a body.
The high-voltage drivetrain includes the battery, charging sockets and e-drive units . Components that are operated with low voltage, such as the headlights, screens and the trailer coupling, are part of the functional mock-up. Driving robot “James” is in the driver’s seat of the 12-volt mock-up, while “Erica”, the interface to the test bench, sits in the rear. “James” offers the experts the opportunity to drive predefined test sequences fully automatically with route profiles taken from real-world scenarios also being run on the test bench.
In particular, the wiring harness and control units can be tested in interaction with real sensors, actuators and other subsystems and power users and checked for efficiency. All parts of the test setup are easily accessible so that pre-series components can be replaced with series parts during the development process. This means that hardware and software components can be put into operation at a very early stage. The full vehicle system test bench can also be used to demonstrate new software versions, which experts refer to as release strokes.
In addition to the FVS, the vehicle powertrain test bench (F-ATS) complements the test portfolio at the ESH. Controlled by “James”, specific maneuvers can be carried out automatically in all conceivable climate zones. Testing across the entire vehicle network eliminates the need to simulate missing vehicle components. The so-called R2R control (Road to Rig) enables the vehicle behavior to be precisely reproduced from the road. This means that the maturity level of the vehicles can be further advanced in the development phases with test vehicles. Preliminary runs of the 24-hour drive in Nardò took place on the F-ATS.