How Long Does It Take To Make A Car
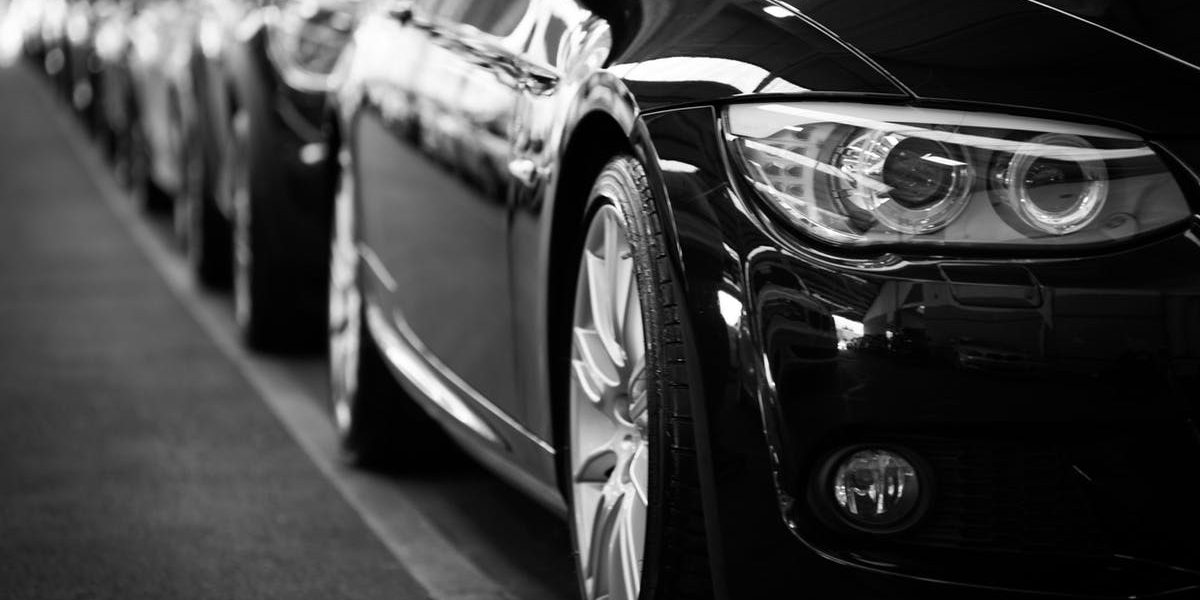
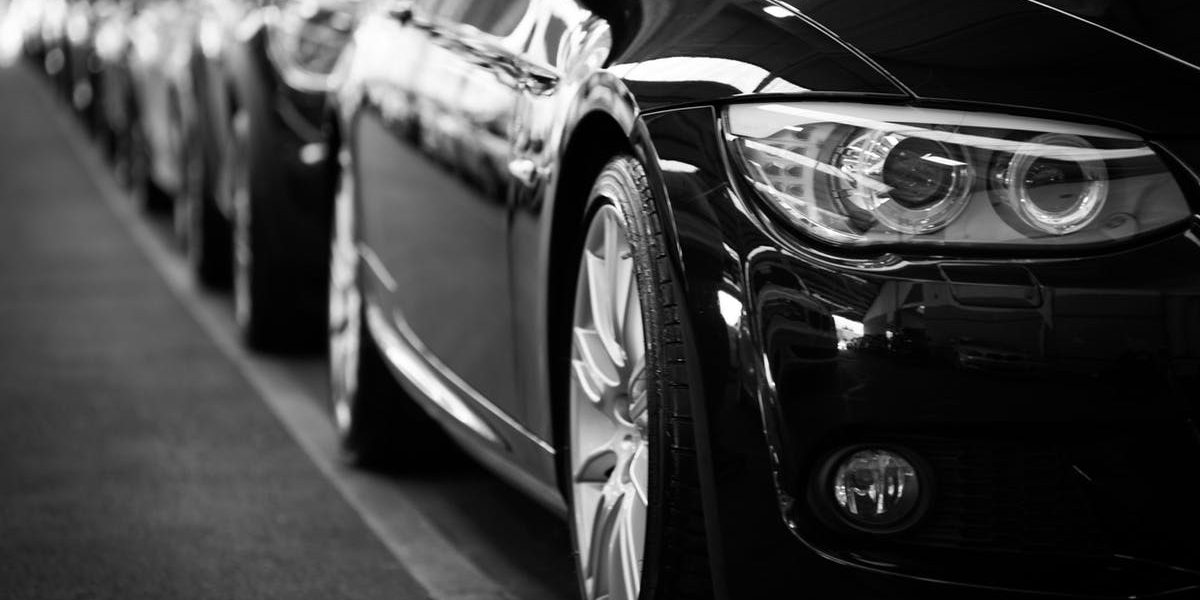
Car Manufacturing Process
To understand the car manufacturing process with its various stages, such as the design process, prototyping, testing and approval, parts, material acquisition, and assembly line production. Each sub-section plays an essential role in bringing the final product to market.
Design Process
The conception process of automobile production involves several phases that ultimately lead to the creation of a vehicle with improved performance and safety features. The design process includes conceptualisation, research, sketches, and modelling to create a viable blueprint. Furthermore, it involves the integration of technological innovations into the car’s design, such as automation and artificial intelligence.
To ensure a successful design process and bring an intuitive user interface to life, designers need to pay attention to industry trends while staying true to their vehicle’s overall vision. By using modern software tools like CAD (computer-aided design), designers can build precise models that optimise safety while balancing other factors such as weight distribution and fuel efficiency.
Moreover, in this process lies the possibility of innovative ideas that will improve road safety by integrating original features into new designs. Whether it is an improvement in energy efficiency or new smart tech features, there is always room for growth in car design.
Pro Tip: Involving multiple departments during the ideation phase allows for an early understanding of cost implications and ensures seamless execution during mass production.
Prototyping
1. A key aspect of the car manufacturing process involves creating a preliminary version through a process known as model testing.
2.
Prototyping |
---|
Development and testing of preliminary models for new vehicle designs. |
3. Prototyping is an essential step in the car manufacturing process, as it allows for extensive testing and adjustments to be made to the design before it enters full-scale production. This reduces costs and ensures that the final product meets all performance and safety standards.
4. When prototyping, it’s important to gather feedback from stakeholders, including designers, engineers, and suppliers, to ensure that all aspects of the design are taken into consideration before moving on to full-scale production.
Testing and Approval
The process of conducting extensive testing and receiving necessary approvals is a crucial part of car manufacturing. An in-depth assessment of various aspects, including safety measures, technical specifications, and environmental impact, must be conducted before approval can be granted.
The car prototypes go through rigors testing to ensure they meet safety and quality standards set by regulatory bodies. Crash tests evaluate the vehicle’s ability to withstand various impacts, while emission tests assess the level of harmful gases released into the environment. The car’s overall performance is tested as well, including acceleration, braking, handling, and noise levels.
Following the comprehensive tests, results are submitted for approval from authorised personnel. Once approved, the car design and materials used will undergo further evaluation to verify their safety aspects.
All stages must be carried out meticulously to ensure manufacturing meets global standards and receives approval from regulatory authorities.
Pro Tip: Manufacturers must prioritise an in-depth understanding of the testing process to fulfil legal regulations.
Parts and Material Acquisition
To ensure the smooth production of cars, the acquisition of necessary parts and materials is crucial. The following table depicts the essential components for car manufacturing and their sources:
Component | Source |
---|---|
Engine parts | Various suppliers |
Electrical system | Specialised electronic manufacturers |
Chassis frame | In-house production or outsourcing |
Tires | Tyre manufacturers and distributors |
Interior upholstery | Speciality textile providers |
It is important to note that acquiring high-quality materials enhances the durability and safety of cars.
Pro Tip: Maintaining a good relationship with reliable suppliers ensures timely delivery and quality products. Assembling cars may seem like a tedious process, but watching it in action can be strangely satisfying—like adult Lego.
Assembly Line Production
Production using a Continuous Moving Conveyor
Car manufacturing involves the use of a conveyor system for mass production, which is called a ‘Continuous Moving Conveyor.’ It is an automated process that moves the car parts along the assembly line through workstations, where different tasks are performed to complete the vehicle.
Steps Involved in Assembly Line Production:
- The body of the car is assembled.
- The engine and transmission systems are fitted.
- Electrical components, like wiring and batteries, are installed.
- Doors, windows, and other exterior features are added.
- Seating upholstery, dashboard components, and audio systems are put in place.
- A quality inspection is done before packing for shipment.
The completion of each step moves the vehicle along the assembly line to the next station, ultimately producing a ready-to-drive car at the final inspection stage without idle time or delays on any particular task or at any workstation.
Moreover, by implementing lean methodologies during this production process, manufacturers can considerably boost their efficiency while reducing their waste output.
Fun Fact: According to the Statista Research Department, “As of 2020, Toyota was the number one automobile manufacturer worldwide with over ten million units sold.”
Timeframe for Making a Car
To better understand the time frame for making a car, consider designing, prototyping, testing, approval, parts and material acquisition, and assembly line production as solutions. These sub-sections are key stages in the production of a car that determine the overall time it takes to manufacture a car.
Time Required for Designing
Designing a car is a crucial and intricate process; thus, it requires time and precision to execute efficiently. To ensure that the design meets the required standards, here is a step-by-step guide on how long it takes to create a car’s design.
- Identification of Goals: The initial phase involves identifying the project objectives and goals, such as aesthetic appeal, performance specifications, fuel economy, etc.
- Brainstorming/Research Stage: At this stage, designers research multiple concepts and explore different design ideas to select the best one that aligns with project objectives.
- Sketching/Ideation: This step entails creating various iterations of sketches to experiment with diverse design schemes.
- Development/3D modelling: The next stage is more technical as designers use advanced computer-aided design software (CAD) to create 3D models of the designs developed in the sketching stages accurately.
- Evaluation and Finalisation: In this final stage, designers review their work extensively until they are satisfied with the outcome and analyse possible faults and potential benefits before submission to production teams.
Beyond estimation from company experience or information gathered online, other factors may impact the design duration. Such factors could include seasonality or holidays that affect manufacturers’ supply chains or difficulties in acquiring necessary raw materials on short notice due to global logistic problems resulting from pandemics like COVID-19.
It would be prudent for companies creating designs for cars to invest in strategies that can mitigate such constraints by forecasting alternate raw material sources and implementing efficient scheduling solutions. Also, utilising e-learning applications and emerging technologies like artificial intelligence and machine learning (AI/ML) models can help boost productivity during shortages. Ultimately, these efforts will make design more efficient while maximising profits over time.
Time Required for Prototyping
Professional Timeframe for Developing a Car Prototype
The duration required for creating a car’s prototype varies according to the design and engineering complexities. The design phase can take around 6–12 months, while the engineering stage needs 12–24 months, and testing may take up to 6 months.
Phase | Duration (Months) |
---|---|
Design | 6-12 |
Engineering | 12-24 |
Testing | Up to 6 |
During the prototyping phase, engineers perform various tests and checks to gauge key parameters like durability, safety, aerodynamics, energy consumption, etc. They optimise designs, materials, and processes continuously based on these results.
Pro Tip: To shorten the product development timeline without compromising quality, use rapid prototyping techniques like 3D printing or CNC machining instead of traditional methodology.
Time Required for Testing and Approval
Car Testing and Approval Timeframe
The time required for car testing and approval can vary depending on a multitude of factors, such as the type of vehicle, its features and complexity, and the regulations in place. However, there is a general timeframe that manufacturers must adhere to to ensure their vehicles meet safety standards.
A table showcasing the time taken for various tests and approvals required for vehicles is as follows:
Test/Approval | Time Taken |
---|---|
Crash Testing | 2-3 weeks |
Emissions Testing | 1-2 months |
Noise Testing | 2-3 weeks |
Safety Standards | Up to 1 year (dependent) |
It can take up to a year or more for safety standard approval, while emissions testing typically takes one to two months. This timeframe also includes assessing whether the vehicle complies with government regulations.
Beyond standard testing and approval procedures, manufacturers must consider unique variables that may impact their timeline. Design changes mid-production or supply chain interruptions can easily add additional days or even weeks to an already tight schedule.
According to the National Highway Traffic Safety Administration (NHTSA), over 38,000 people lost their lives due to car accidents in 2019 alone. Automobile manufacturers need to invest adequate time and resources in ensuring their products are safe for consumers before releasing them into the market.
Time Required for Parts and Material Acquisition
The Timeframe for Acquiring Parts and Materials in the Manufacturing of a Vehicle
Acquiring parts and materials is an essential process that takes place during the manufacturing of a vehicle. It is estimated that this process takes several weeks to months, depending on various factors.
To better understand the time required for acquiring parts and materials during vehicle manufacture, we have created the following table:
Components | Estimated Time |
---|---|
Engine and Transmission | 4-6 weeks |
Chassis and Suspension System | 6-8 weeks |
Braking system | 3-4 weeks |
Electrical components | 3-5 weeks |
Interior and Exterior Design | 2-3 months |
As seen in the table, different components take varying amounts of time to acquire. It also depends on geographical locations, weather conditions, and other aspects of supply chain management.
While manufacturing a vehicle, it’s important to note that some components require less lead time than others; thus, proper planning must be implemented before initiating production.
It is noteworthy that some companies overestimate their lead times as part of their marketing strategy. One interesting example is when Ford announced in 1980 that it would only be building “custom-ordered” vehicles, consequently generating buzz around its brand, which resulted in high sales volumes.
Time Required for Assembly Line Production
The production timeline of assembling a car through an assembly line is an essential process that involves various stages of manufacturing. The duration of each stage depends on the level of complexity involved in assembling each car part. A single vehicle’s manufacturing process takes anywhere from 10 to 36 hours, which varies from model to model and company to company.
Stage | Timeframe |
---|---|
Welding body parts together | 3-4 hours |
Installation of Mechanical Parts | 4-5 hours |
Painting the Car Body | 1-2 days |
Interior Fitting | 5-6 hours |
The timeframe required for assembly line production is determined based on multiple factors, including the sophistication and intricacy involved in manufacturing a specific car model. Besides, factors like workload at factories can also impact the duration of making a car.
In recent years, automobile companies have made remarkable progress in reducing production time for cars by investing in tools and technology that streamline the automotive production process. For instance, some factories employ over 600 robots to speed up certain tasks that once required human resources entirely.
It’s worth noting that there are exceptional cases, like Tesla’s Model S being manufactured within three days by converting part of its factory into a super-intensive production zone for seven days. Adoption of such methods can significantly improve productivity if applied accurately.
Factors Affecting the Time Required to Make a Car
To understand what factors can affect the time required to make a car, dive into the section on Factors Affecting the Time Required to Make a Car, with a focus on the number of units to be produced, the complexity of the car design, the availability of parts and materials, production technology and efficiency, the labour force, and skills.
Number of Units to be Produced
To optimise the production process, the quantity of cars to be manufactured plays a significant role. The higher the quantity, the more time and resources are needed for production. Using advanced machinery can significantly reduce production time while also minimising defects.
A key consideration when deciding on this number is demand forecasting; an accurate estimate reduces cost and affects supply chain management long-term.
Pro Tip: Employ a just-in-time inventory system to minimise overstock or run-out risks.
The following table shows the amount of time required and the resources needed to manufacture a certain number of cars:
No. of Units | Average Time Required | Required Resources |
---|---|---|
10 | 1 month | 12 labourers, 1 factory |
100 | 6 months | 100 labourers, 1 factory, additional materials and machines |
1000 | 3 years | 1000+ labourers, multiple factories with expanded infrastructure and resources. |
Complexity of the Car Design
The intricacy of the automobile blueprint influences the duration necessary to manufacture a vehicle. The more complicated the design, the longer it takes to produce.
Type of Design | Average Manufacturing Time (in days) |
---|---|
Simple | 25-30 |
Moderate | 35-40 |
Complex | 45-50 |
Factors that contribute to a car’s intricate design include computerised systems, safety features, and electrical components. These features require additional time to assemble correctly and ensure they function accurately within the vehicle.
With all this in mind, it is essential to consider the complexity of your design before finalising it. Choosing a less complex design can save both time and money while still producing a functional vehicle.
If you’re looking to create a car but are unsure where to start, consider seeking out professional assistance and guidance throughout the process. Regardless of your choice, failing to account for these variables may cause delays and lost opportunities in your project.
Availability of Parts and Materials
The timely availability of necessary parts and materials is an important factor in car production, affecting the overall time required to make a car.
The following table showcases the impact of ‘Material and Parts Availability’ on car production:
Factors | Impact on Car Production |
---|---|
Delayed supply chains | Larger waiting times |
Shortages | Increased assembly duration |
Inadequate quality control | Extended inspection and repair periods |
Unique details that have not been covered include identifying the source of material or part delays that could arise from various reasons, such as natural disasters, pandemics, and international trade issues.
To combat delayed delivery times, manufacturers can opt for multiple suppliers to avoid sole dependency on one supplier. It is also advisable to maintain multiple storage systems at different locations with adequate inventory levels. This could help save time by utilising alternative sources when required. Furthermore, implementing automated systems could aid in maintaining awareness of inventory levels, allowing for adjustments to be made more efficiently.
Overall, achieving efficient material and parts management is essential to maintaining production schedules. Production technology may have improved, but if you’re still taking tea breaks every 10 minutes, then making a car will take longer than building a tea-making machine.
Production Technology and Efficiency
Production efficiency and technology play a significant role in determining the time required to make a car. The use of advanced tools and equipment can significantly reduce production time.
A table indicating the factors affecting production time is shown below:
Factors | Production Time |
---|---|
Assembly Line Length | A longer line means increased Time |
Skilled Workers | Lesser training time = Decreased Time |
Use of Robotics | More automated = Decreased Time |
Inventory Availability | Adequate Inventory = Decreased Time |
The above table illustrates that the length of the assembly line increases the production time, while the availability of skilled workers who need less training can reduce it. Additionally, using robotics for automated work can also have a positive impact on decreasing overall production time.
Pro Tip: A proper balance between manual labour and automation can help increase productivity and efficiency in car manufacturing.
Labour Force and Skills
The human workforce employed in car manufacturing plays a significant role in determining the time required to make a car. The skill set of the workers can determine the speed and efficiency at which they work. Skilled workers can complete individual tasks quickly, allowing for faster overall completion of the vehicle.
Additionally, labour force management can also impact the time required to manufacture a car. Proper scheduling and allocation of tasks among workers can lead to smoother production processes and eliminate delays caused by worker unavailability.
Furthermore, training programmes for workers can improve their skills and decrease production time as they become more familiar with the tools and processes involved in manufacturing cars.
Comparison with Other Vehicles Manufacturing Timeframes
To better understand the time frame of car manufacturing, let’s compare it to other vehicle manufacturing processes. This will provide a clear idea of how long it takes to manufacture a car in comparison to other types of vehicles. We’ll explore the manufacturing processes of trucks, motorcycles, bicycles, and aircraft as potential comparisons for car manufacturing times.
Truck Manufacturing Process
The production process of heavy vehicle manufacturing is of the utmost significance in the automobile industry. To give you an idea of how truck manufacturing takes place, here’s a brief overview.
Manufacturing Stage | Timeframe (in days) |
---|---|
Production Planning and Preparation | 30-45 |
Framing and Body Assembly | 15-20 |
Cab Assembly and Fitting Accessories | 10-15 |
Painting and Polishing | 7-10 |
Interestingly, a truck requires around fifteen to twenty days to manufacture its frame and body assembly. It takes another ten to fifteen days to assemble the cab and fit accessories. However, painting takes merely seven to ten days before final inspection.
It’s interesting to note that while the majority of heavy vehicles take months or years for production from initial design until they hit the road, trucks have a relatively shorter timeframe. The manufacturing speed proves their essentiality in businesses as well as their importance in supply chain management.
According to Business Insider, it takes General Motors Company approximately two weeks of sequential manufacturing steps before finally introducing finished GMC Sierra or Chevrolet Silverado trucks into market circulation.
Motorcycle Manufacturing Process
Starting with the motorcycle manufacturing process, involves various stages, including designing, engineering, assembling, testing, and shipping the final product to customers. The entire process demands a high level of precision and skill to maintain quality while meeting production timelines.
To better understand the motorcycle manufacturing process, let’s turn our attention to a table that provides an overview of manufacturing timeframes for different modes of transportation.
Transportation Mode | Production Timeframe |
---|---|
Car | 12-16 weeks |
Truck | 18-24 weeks |
Motorcycle | 4-6 weeks |
As seen from the table above, motorcycles take the shortest time to manufacture compared to cars and trucks. The reason behind this is that motorcycles have comparatively fewer parts and require less complex machinery for assembly.
While discussing the unique details of this process, it’s essential to mention that many factors, such as raw material availability and demand fluctuations, can impact production timelines. Given these uncertainties in supply chain management, manufacturers need to strategize production planning accordingly.
In light of these details and the challenges faced by manufacturers during the motorcycle manufacturing process, we propose two suggestions: 1. Investing in automation technology can streamline processes and improve efficiency while reducing labour costs. 2. Adopting an agile production approach with flexible scheduling arrangements can help manufacturers adapt quickly and keep up with rapidly changing market conditions.
Bicycle Manufacturing Process
The production procedure of a popular and eco-friendly mode of transportation, the bicycle, can be observed as follows:
Stages | Duration (hours) |
---|---|
Frame manufacturing | 4 |
Wheel assembly | 1 |
Brake system installation | 2 |
Lubrication and final inspection | 1 |
Interestingly, in comparison to vehicles such as cars and trucks, bicycles take less time to manufacture and assemble, which reflects their simplicity in design. Additionally, these vehicles are versatile in carrying people and objects over short distances making cycling a popular choice for everyday commuting.
It is important to note that throughout history, bicycles have undergone numerous transformations in their designs. Innovations have emerged targeting specific use cases within racing or leisure activities creating further differentiation across different niches.
At one point during the late 19th century, bikes became more affordable due to the mass production techniques made possible by inventions like the chain-driven bicycle. The outcome was an increase in demand for cycle transport worldwide that enabled even more designs and technological advancements to emerge.
Aircraft Manufacturing Process
Aircraft Production Procedure
Aircraft manufacturing involves complex and intricate procedures that span over several stages. The process consists of many intricate parts that must be integrated flawlessly to ensure peak performance.
The following table outlines the approximate timelines for various types of vehicles, including aircraft, cars, and ships.
Vehicle | Manufacturing Timeframe |
---|---|
Boeing 767 | 10 months |
Airbus A380 | 11 months |
Car | 13 hours |
Cruise Ship | 3 years |
It’s interesting to note that while cars can be manufactured in just a few hours, cruise ships can take up to three years before they’re ready for use.
One unique aspect of aircraft manufacturing is its focus on safety regulations. Each stage of the production process undergoes rigorous quality checks to ensure that each component meets aviation standards.
For successful aircraft manufacturing outcomes, it’s essential to invest in modern technology and adequate workforce resources. Additionally, regular training and development programs should be put in place to keep up with innovative advancements in aviation technology.
Future Trends in Car Manufacturing
To learn about the future trends in car manufacturing, delve into the section called “Future Trends in Car Manufacturing” with a focus on Automation and Robotics, Sustainable Manufacturing Practices, Customization and Personalization, New Materials and Design Techniques, and Integration of Advanced Technologies. This section will give you insights into where the car manufacturing industry is headed in the upcoming years.
Automation and Robotics
The use of intelligent automation and robotics in the production of vehicles is a prominent trend.
The table below exhibits the application of automation and robotics in car manufacturing. Column one represents the automobile part or process that requires automation and robotics while column two shows how it is facilitated by machines:
Process/Part | Automation/Robotics |
---|---|
Welding | Spot, arc, laser welding robots |
Painting | Paint mixing, spraying robots |
Component assembly | Assembly robots |
Inspection/Testing | Automated inspection/testing machines |
Moving forward, this technology reduces human error by making precise actions. Precision ensures efficient consistency hence higher production rates without compromising quality.
For optimal results using this technology, manufacturers should invest in creating an automated supply chain for materials through sensors and real-time data exchange. In addition to that, programming predictive maintenance protocols for these machines will reduce costly downtimes hence saving significant revenue.
When it comes to sustainable manufacturing practices in the car industry, it’s not just about reducing carbon emissions, but also about making sure the workers aren’t left feeling exhausted and wanting to drive off a cliff.
Sustainable Manufacturing Practices
Incorporating eco-friendly practices in the automotive industry is imperative. This includes using renewable energy, reducing waste, recycling materials, and minimizing carbon emissions during production. Adopting sustainable manufacturing methods can significantly reduce the environmental impact of car manufacturing.
Implementing a circular economy approach in car manufacturing can induce sustainability in the industry. This involves designing products with recycled materials and creating closed-loop supply chains to minimize waste generation. Additionally, electric vehicles and autonomous driving technologies can further improve sustainability in car manufacturing.
To achieve sustainable manufacturing practices, automakers need to establish partnerships with suppliers for sourcing sustainable materials. The use of 3D printing technology and artificial intelligence can optimize energy consumption during production processes. Additionally, implementing efficient logistics and transport systems can reduce carbon footprint during distribution.
According to the U.S. Department of Energy (DOE), producing an electric vehicle generates up to 56% less greenhouse gas emissions than producing a traditional gasoline-powered vehicle.
Sustainable automotive manufacturing practices are necessary for reducing environmental impacts while maintaining high-quality production processes that lead to long-term benefits for consumers and society as a whole.
Customization and Personalization
The personal touch has become a driving force in the automotive industry. The ability to cater to individual preferences is a key aspect of car manufacturing today.
- Personalization options are essential for brand differentiation and creating emotional connections with customers.
- Customization offers consumers more control over the design, features and performance of their vehicles.
- The rise of 3D printing is enabling greater customization, with the potential for on-demand parts production.
It’s not just about adding fancy paint jobs anymore. The possibilities range from custom interiors to tailored technology solutions. With increasing technological advancements, customization and personalization will continue to shape the future of car manufacturing.
A prime example is how Tesla offers software updates that enable consumers to upgrade their cars’ performance or add new features remotely. Perhaps someday every aspect of a vehicle can be personalized, including its AI assistant personality.
The idea of personalized cars may seem relatively modern, but it’s been around since Henry Ford rolled off the first Model Ts in black only. As soon as different coloured paints were invented, custom paint jobs became popular. It’s safe to say that customization has come a long way since then, with new technologies shaping the future trends in car manufacturing.
New Materials and Design Techniques
In the ever-evolving field of car manufacturing, there is a constant push towards exploring innovative materials and design techniques that will revolutionize the industry. The following table outlines some of the latest advancements under the subject of ‘Novel Materials and Enhanced Design Methods’.
New Materials | Design Techniques |
---|---|
Graphene | 3D Printing |
Carbon Fiber | Machine Learning |
Ceramic Matrix | Virtual Reality |
Graphene, with its exceptional strength-to-weight ratio, has shown promising results in enhancing fuel efficiency. Carbon fibre is being used to manufacture lightweight components in cars without compromising their structural integrity. Ceramic Matrix composites are finding use in high-temperature applications in vehicles’ exhaust systems.
In addition, 3D printing is becoming more common as it allows the development of complex structures quickly and economically. Machine learning algorithms help optimize designs by predicting performance outcomes while taking into account various parameters. Virtual Reality, enables designers to visualize and refine concepts before creating physical prototypes.
To keep up with these advancements, manufacturers should focus on investing in research and development efforts aimed at integrating these new materials and design techniques while also keeping costs relatively low. They can also collaborate with suppliers specializing in niche materials to obtain a competitive edge over rivals.
Thus, these novel materials coupled with enhanced design methods are set to usher us into a new era of car manufacturing.
Integration of Advanced Technologies
Advanced Automotive Technologies Integration
The integration of advanced technologies in car manufacturing has enhanced vehicle performance and safety. Car makers are continuously exploring new techniques for incorporating advanced technologies into their products to enhance customer experiences.
Below is an overview table depicting actual data about the integration of advanced automotive technologies:
Technology | Benefits |
---|---|
Artificial Intelligence | Improved routing, fuel efficiency, and safety |
IoT | Enables vehicle-to-vehicle (V2V) communication |
Autonomous Driving | Reduced accidents, improved traffic flow |
In addition to these popular advancements, additive manufacturing techniques allow for the 3D printing of automotive components such as lightweight engine blocks and specialized braking systems.
Did you know that Tesla’s self-driving Autopilot system uses machine learning algorithms for real-time image recognition?
How Long Does It Take To Make A Car – Frequently Asked Questions
1. How long does it take to make a car from scratch?
It typically takes around 12-18 hours to build a car from scratch. However, this can vary depending on the complexity of the car and the efficiency of the manufacturing process.
2. How long does it take to assemble a car in a factory?
The average time it takes to assemble a car in a factory is around 15-20 hours. However, this can also vary depending on the type of car being built and the production methods used.
3. How long does it take to build a prototype car?
Building a prototype car can take anywhere from a few weeks to several months. This process involves designing and testing various components and systems before assembling them into a functioning vehicle.
4. How long does it take to build an electric car?
Building an electric car can take anywhere from 6 months to a year. This is because electric cars require specialised components and systems, such as batteries and electric motors, which can take longer to manufacture and assemble than traditional combustion engines.
5. How long does it take to build a luxury car?
The production of luxury cars can take anywhere from a few weeks to several months. Luxury cars typically require high-end materials and specialised customisation, which can add to the production time.
6. How long does it take to build a race car?
The production of a race car can take anywhere from 3-6 months. These cars require specialised components and systems, such as aerodynamic designs and high-performance engines, which can take longer to manufacture and assemble than standard production vehicles.